Конструкционные материалы для изготовления ЛА
Появление новых конструкторских идей всегда сопровождается постановкой новых проблем в области материаловедения. Наиболее обоснованные рекомендации по применению новых материалов могут быть выданы при условии анализа их свойств и технологических возможностей, а также конструктивных особенностей изделий, в которых они применяются. Возрастающие темпы увеличения грузооборота на воздушных линиях требуют использования широкофюзеляжных грузовых и пассажирских самолетов с числами Маха М = 0,9...0,95. Уровень шума и расход топлива у широкофюзеляжных самолетов меньше, чем у самолетов предыдущих поколений. Совершенствование широкофюзеляжных самолетов в основном идет по пути повышения экономичности, эффективности, надежности, ресурса, маневренности, снижения шума в салоне и на взлетной полосе аэродрома и уменьшения загрязненности окружающей среды.
Сравнительный анализ последних технических достижений в области аэродинамики и электроники показывает, что наиболее перспективным с точки зрения повышения эффективности летательных аппаратов - ЛА является снижение массы конструкции путем использования ПКМ, порошковых (гранулированных) алюминиевых сплавов и алюминиево-литиевых сплавов. Для оценки эффективности применения новых материалов необходимо знать, как отразится замена ими ранее применявшегося материала на характеристиках агрегата и изделия в целом.
Применяемые в конструкциях ЛА материалы можно разделить на три группы.
Первая группа включает металлические славы на основе алюминия и титана. Из материалов этой группы изготовляются фюзеляж, крыло, оперение, агрегаты механизации крыла, а также посадочные устройства.
В зависимости от назначения ЛА и его летно-технических данных состав этих материалов и их масса в конструкции ЛА могут изменяться в довольно широких пределах. Так, в широкофюзеляжных самолетах с М = 0,9...0,95 в качестве основного конструкционного материала используются алюминиевые сплавы, а в самолетах с М < 2 - теплостойкие стали и титановые сплавы. К этой группе конструкционных материалов также относятся металлические композиционные материалы. В последние годы с развитием металлургической технологии их создание пошло по пути включения в основной конструкционный материал материалов других марок в виде отдельных слоев или утолщенных плакировок.
Ко второй группе относятся ПКМ. Эти материалы по сравнению с материалами первой группы, имеют ряд преимуществ, позволяющих значительно повысить эффективность конструкций. Наиболее перспективные с точки зрения снижения массы конструкции и стоимости являются ПКМ на основе полимерных органических и углеродистых волокон, т.е. органопластики и углепластики. Внедрение в конструкцию модификации вертолета SH-53D ПКМ позволило на 507 кг (на 18,5%) снизить массу планера по сравнению с массой планера первоначального варианта этого вертолета, на 80% выполненного из алюминиевых сплавов. На вертолете SH-47 этой же фирмы использование ПКМ обеспечило снижение массы планера на 10%, что позволило повысить его грузоподъемность на 30% и на 40%увеличить дальность полета.
Снижение массы позволило использовать полученный резерв для совершенствования характеристик ЛА, для увеличения дальности полета при сохранении начальной взлетной массы, для увеличения полезной нагрузки при сохранении той же дальности полета, для уменьшения линейных размеров, материалоемкости, отношения массы конструкции к полезной массе и мощности (тяге) и т.д.
Применение в конструкции самолета 40...50% ПКМ позволяют снизить массу пустого самолета на 30% и добиться наибольшей экономии при минимальных эксплуатационных расходах. Например, замена в конструкциях планера пассажирского самолета массой 160 т 20% массы материалов первой группы на ПКМ позволяет снизить массу самолета на 17% и повысить полезную нагрузку на 20%.
Для получения экономического эффекта от использования ПКМ следует учитывать не только их стоимость, но и преимущества, которые можно получить при их рациональном применении. Использование ПКМ позволяет снизить расход энергии, трудоемкость изготовления ЛА, повысить его комфортабельность, надежность и долговечность.
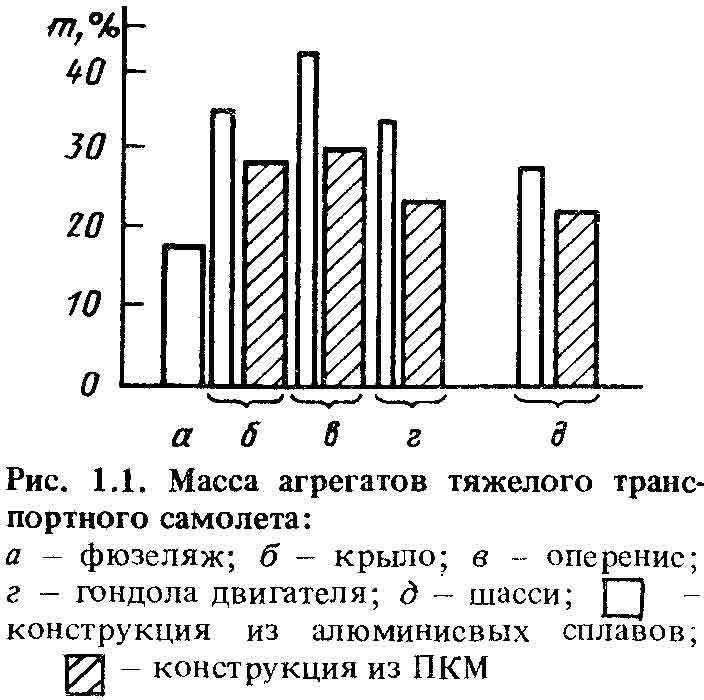
На рис. 1.1 приведена масса агрегатов тяжелого транспортного самолета, изготовленных из алюминиевых сплавов и ПКМ. Использование ПКМ позволяет уменьшить число деталей. Так, элерон клепаной конструкции, изготовленный из алюминиевого сплава, для самолета Локхид L-1011 состоит из 227 деталей, а элерон из ПКМ состоит из 45 деталей (рис. 1.2). Замена элерона из алюминиевого сплава на элерон из ПКМ позволила получить экономию в массе в пределах 28%.
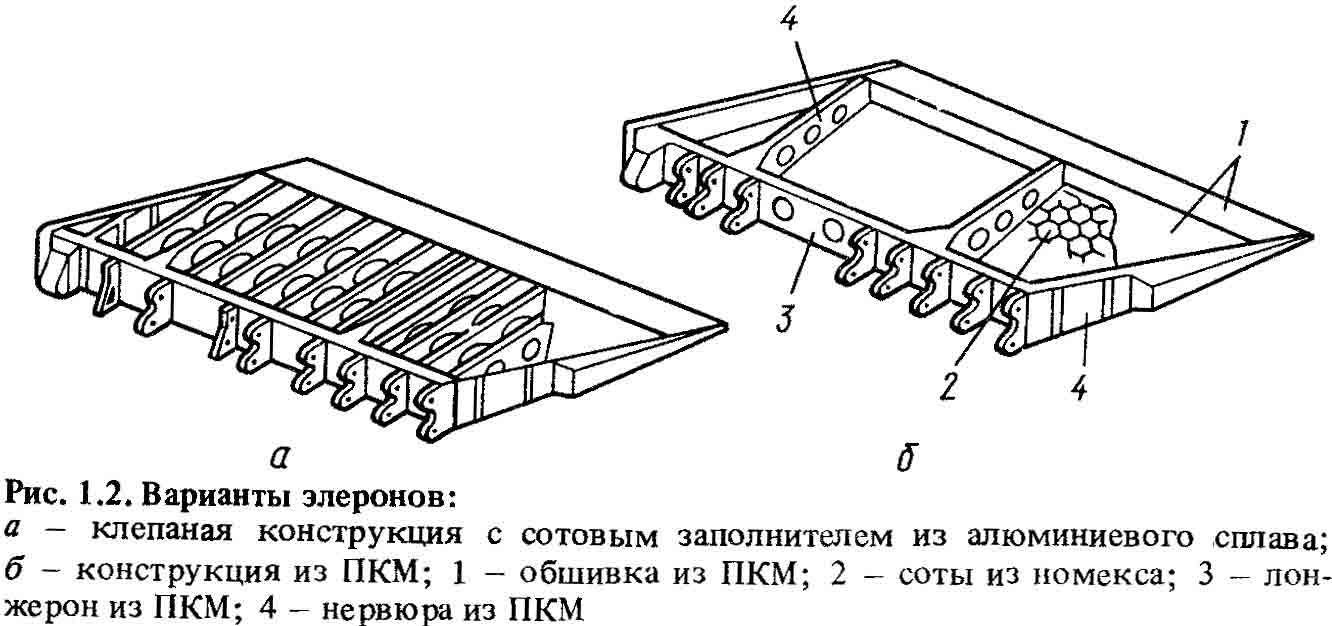
Киль самолета Локхид L-1011, изготовленный из ПКМ, имеет массу на 27% меньше массы киля, изготовленного из алюминиевых сплавов. Эффективность элементов из ПКМ зависит от методов проектирования. Исследование, проведенное фирмой "Грумман", показывает, что при прямой замене металла в конструкциях самолета на ПКМ снижение массы составляет 13%, при этом максимальная взлетная масса уменьшается всего на 6%. При замене металла на ПКМ удается уменьшить также размеры изделий.
К третьей группе материалов можно отнести различные неметаллические конструктивно-декоративные материалы: полиамиды, пенопласты, пресс-материалы, полистиролы, резины и др. Состав материала третьей группы определяется типом самолета, вертолета.
Масса деталей из неметаллических материалов второй и третьей групп в зависимости от типа самолета может быть в пределах 13...20% от массы самолета. Основа ПКМ, входящих во вторую группу, вследствие своей химической активности в процессе термообработки или без нее отверждается под действием активаторов. В результате склеивания (химического соединения основы и армирующего материала) линейные молекулы приобретают пространственно-сетчатую структуру и необходимое термостабильное состояние. Используемые эпоксидные основы обычно полимеризуются при 127...179°С, и их характеристики во многом зависят от температуры полимеризации и вводимых для пластификации, улучшения реологических характеристик и контроля текучести в процессе формообразования добавок.
Механические свойства материалов второй группы определяются, прежде всего, исходной прочностью основы, а также маркой армирующего материала и степенью армирования основы. При нагружениях внешние нагрузки на основу передаются через касательные напряжения сдвига. Основа нагружается постепенно.
Максимальное напряжение τmax зависит от прочности связи между армирующими элементами — адгезионной и когезионной прочности.
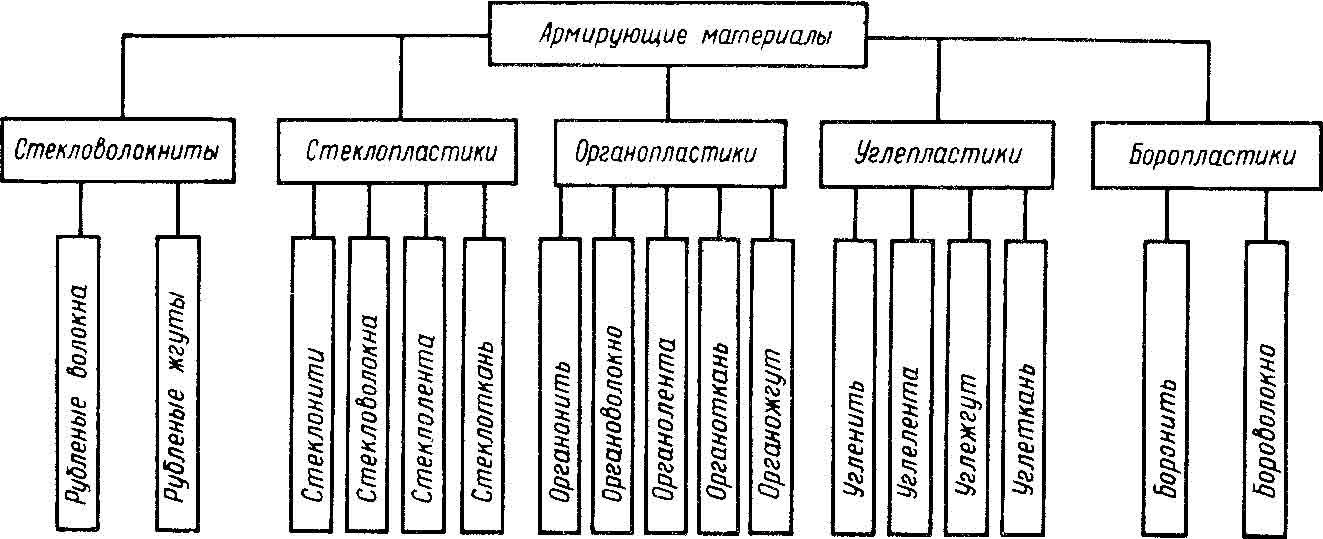 Рис. 1.3. Основные виды армирующих материалов
Механизм разрушения (после разрыва одного или нескольких волокон) будет заключаться либо в разрушении адгезионной связи (если основа хрупкая), либо в пластическом деформировании (если основа пластичная). Для каждого типа основы следует выделять комплекс свойств, которыми она должна обладать для обеспечения максимальной прочности ПКМ. В качестве армирующих материалов используются (рис. 1.3) :
1. Стекловолокниты — это материалы с хаотически расположенными штапельными волокнами длиной 50...500 мм и жгутами длиной 50....100 мм. Стекловолокниты изотропны, но их механические свойства недостаточно хороши, и поэтому с применением этих материалов изготавливаются в основном малонагруженные детали.
2. Стеклопластики — это материалы, в которые входят стеклянные нити, волокна, ленты, а также ткани полотняного или сатинового переплетения. ПКМ с основой из стеклопластиков обладают высокой механической прочностью, а поэтому из них изготавливаются детали, воспринимающие аэродинамические нагрузки (обтекатели, зализы, крышки люков и др.).
3. Органопластики — это материалы с органическими волокнами, лентами, нитями, жгутами и тканями. Органопластики относятся к легким материалам, их плотность равна 0,95...1,4 кг/см3. Одним из основных показателей работоспособности органопластиков является ползучесть. По удельной жесткости органопластики в 2 раза превосходят стеклопластики, но при этом в 1,5...2,0 раза уступают угле- и боропластикам. В зарубежных конструкциях широко используется органопластик кевлар различных модификаций. Волокна кевлара часто называют арамидными. К арамидным волокнам относятся фениленизофталамиды номекс, конекс, фенилон; амидгидразиды, кевлар, а также аренка. Характеристики арамидных волокон приведены в табл. 1.1.
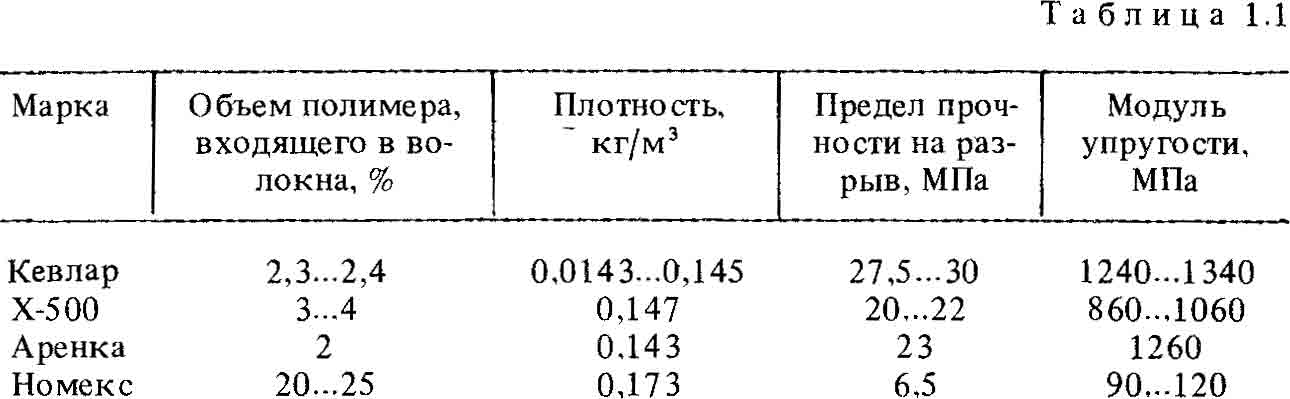
При сжатии характеристики органопластиков меняются, в результате чего создаются новые материалы.
Органопластики обладают хорошими теплоизоляционными свойствами - их тепло- и температуропроводности в два раза ниже, а удельная теплоемкость на 50...70 % выше, чем у стеклопластиков. Механические характеристики органопластиков приведены в табл. 1.2.
Органопластики легкие и характеризуются высокой удельной прочностью, хорошими показателями прочности при сжатии, изгибе и сдвиге. Они являются хорошими диэлектриками. Эти материалы устойчивы к действию ударных и знакопеременных нагрузок, они плохо воспламеняются и их характеристики достаточно стабильны при высокой влажности. Органопластики технологичны и легко перерабатываются.
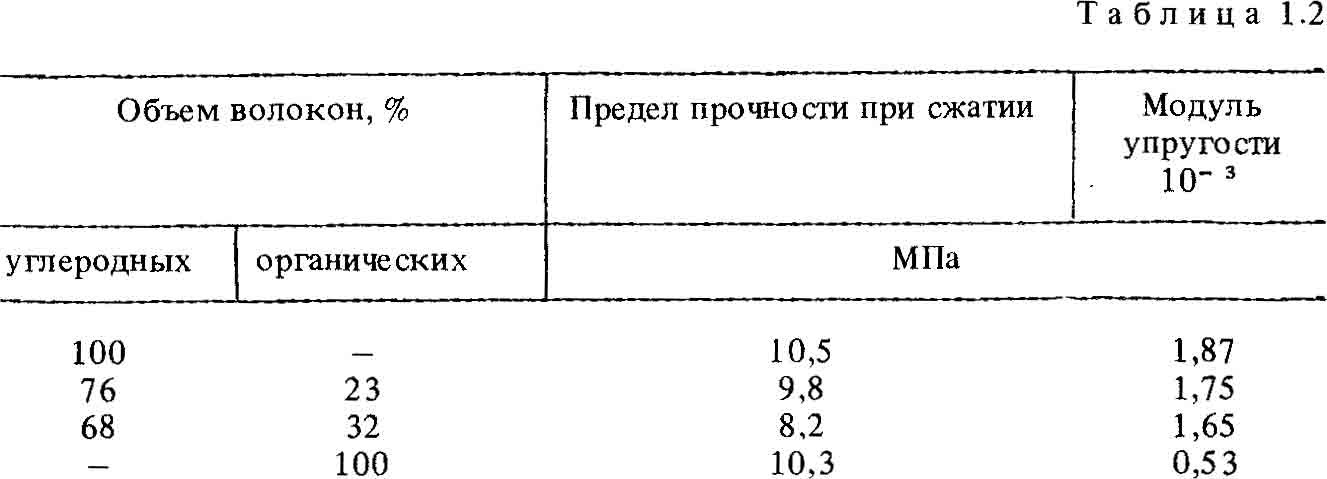
Органопластики благодаря своим физико-механичеким показателям рекомендуются как армирующие элементы в ПКМ, применяемых: в конструкциях, испытывающих предельные растягивающие напряжения, например в сосудах высокого давления;
в деталях и узлах монолитных и слоистых панелей с легкими заполнителями различных типов, испытывающих умеренные нагрузки, например в зализах, обтекателях, панелях; в деталях и узлах декоративных элементов интерьеров самолетов, вертолетов, судов и т.п.; в деталях и узлах электро- и радиотехнического назначения, например в обтекателях для укрытия антенн и т.п.
Применение органопластиков вместо стеклопластиков позволяет: на 20...50 % снизить массу элементов конструкций;
в 5...10 раз увеличить ресурс и повысить надежность работы конструкций, испытывающих воздействие значительных знакопеременных и ударных нагрузок; в 1,5...2 раза повысить тепло-, звуко- и электроизоляционные свойства конструкций; в 3...5 раз снизить трудоемкость изготовления деталей.
4. Углепластики — это материалы с углеродными нитями, волокнами, лентами, тканями. Волокна изготавливаются из полиакрилонитратных заготовок либо из смолы — остатка, образующегося при высокотемпературном расщеплении в процессе переработки нефти.
К основным преимуществам углепластиков следует отнести сравнительно малую плотность, высокие статическое сопротивление усталости, жесткость, сопротивляемость коррозии, износо- и абразивостойкость, малые коэффициент линейного расширения и электрическую проводимость. Наиболее широко применяются волокна из полиакрилонитрильного сырья, имеющего модуль упругости 2,45 • 103 МПа и предел прочности от 32,0 до 39,0 МПа. ПКМ получается путем связывания углеродных волокон с основой, состоящей из некоторых эпоксидных, фенольных, полиэфирных, полисульфонных смол или полифениленового сульфида.
Углеродные волокна можно разделять на три основных класса: высокомодульные, высокопрочные и средней прочности (табл. 1.3).
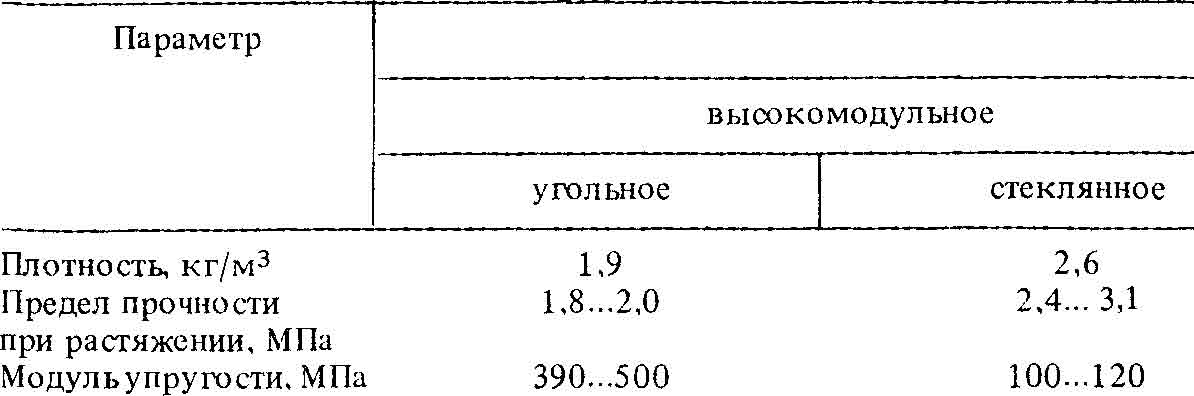
Прочность волокна определяется делением разрушающей нагрузки на площадь его поперечного сечения. Углеродные волокна обеспечивают высокую жесткость контрукции, которая является мерой сопротивляемости материала. Использование углеродных волокон и лент позволяет создавать ПКМ для определенных условий работы.
На характеристики проектируемого ПКМ влияют:
соотношение объемов основы и армирующего материала; число слоев армирующего материала, его марка и его вид (волокно или лента); направление укладки волокон и лент армирующего материала относительно главных действующих нагрузок; технология пропитки армирующего материала основой; технологические процессы изготовления деталей, узлов и агрегатов (формование, намотка и др.).
Углепластики используются с эпоксидной основой. Фенольные смолы не используются для изготовления конструкционных ПКМ, а используются главным образом для получения ПКМ для изготовления деталей оборудования и интерьера пассажирских кабин из-за негорючести. Наибольший интерес в настоящее время представляют бисталеимиды и полиамиды. Бисталеимиды и их различные модификации по стоимости ниже других основ, а посравнению с эпоксидными полимерами имеют более высокие теплоскойкость и вязкость. Они легко перерабатываются и представляются весьма перспективными при получении ПКМ для изготовления силовых конструкций.
Большая работа по исследованию полиамидов проводится в НАСА по программе, цель которой — разработка нового поколения полиамидных углепластиков. Рабочая температура углепластиков при полиамидной основе зависит от продолжительности ее воздействия и равна 480...535°С при кратковременном воздействии, 260...315°С при воздействии в течение 100...1000 ч и 230...260°С при воздействии в течение 50000...70000 ч. ПКМ с углепластиковым армирующим материалом планируется для замены углеэпоксидных ПКМ в изделиях, длительно работающих при температурах 120... 175°С в условиях повышенной влажности [Son D.R. Composites im aircraft construction // Flieght international/ 1981/ Vol. 119, №3759, P.1551-1555].
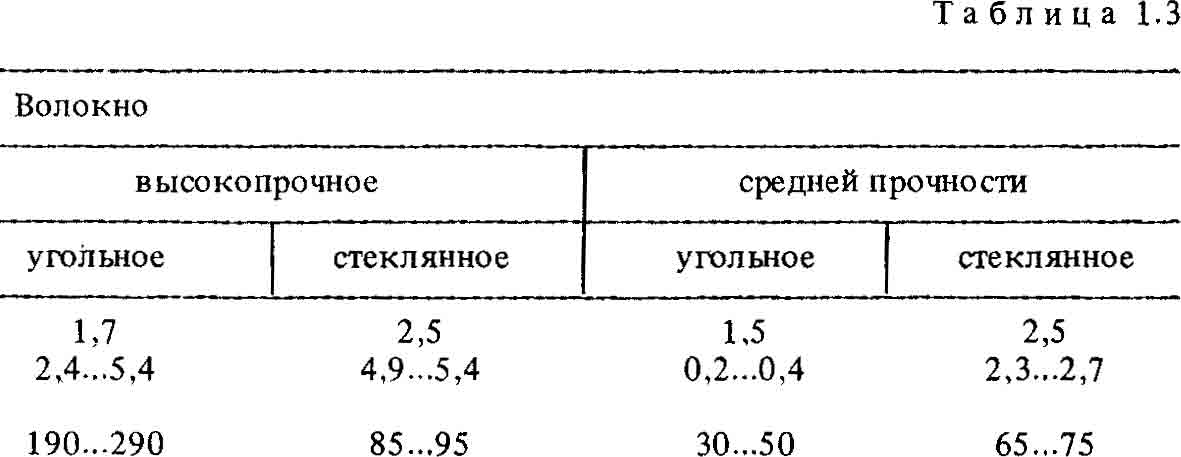
Стойкость к окислению углеродного волокна увеличивается с увеличением модуля упругости, значение которого зависит от температуры графитизации и соответственно содержания углерода.
Влияние теплового старения на воздухе на характеристики углепластика селион при использовании в качестве армирующего материала углеродного волокна показано в табл. 1.4.
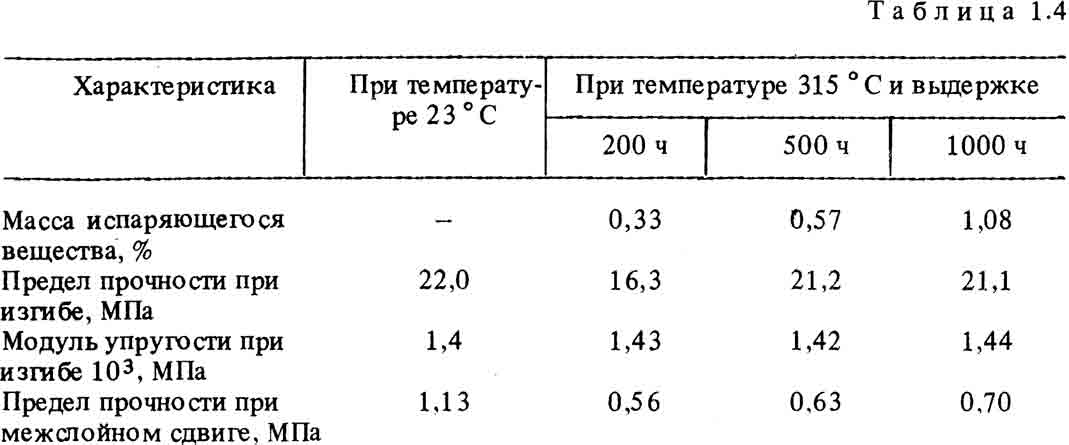
5. Боропластики — это материалы с борными волокнами (волокнами из поликристаллического бора, осажденного на вольфрамовую проволоку) и борными стеклонитями, состоящими из параллельно расположенных борных волокон.
В зависимости от предела прочности при растяжении ов выпускаются борные волокна трех сортов: к 1-му сорту относятся волокна с σв > 32,5 МПа, ко 2-му сорту — с σв = 27,5...32,4 МПа и к 3-му сорту — с σв = 22,5...27,4МПа.
На рис. 1.4 приведена схема укладки слоев борных волокон в обшивке стабилизатора самолета F-14A фирмы "Грумман". Применение ПКМ с боропластиковым армирующим материалом взамен алюминиевых сплавов в сочетании с титановыми сплавами обеспечило снижение массы конструкции на 25%. Этот стабилизатор представляет собой серийный агрегат, изготовленный с использованием ПКМ с боропластиковым армирующим материалом.
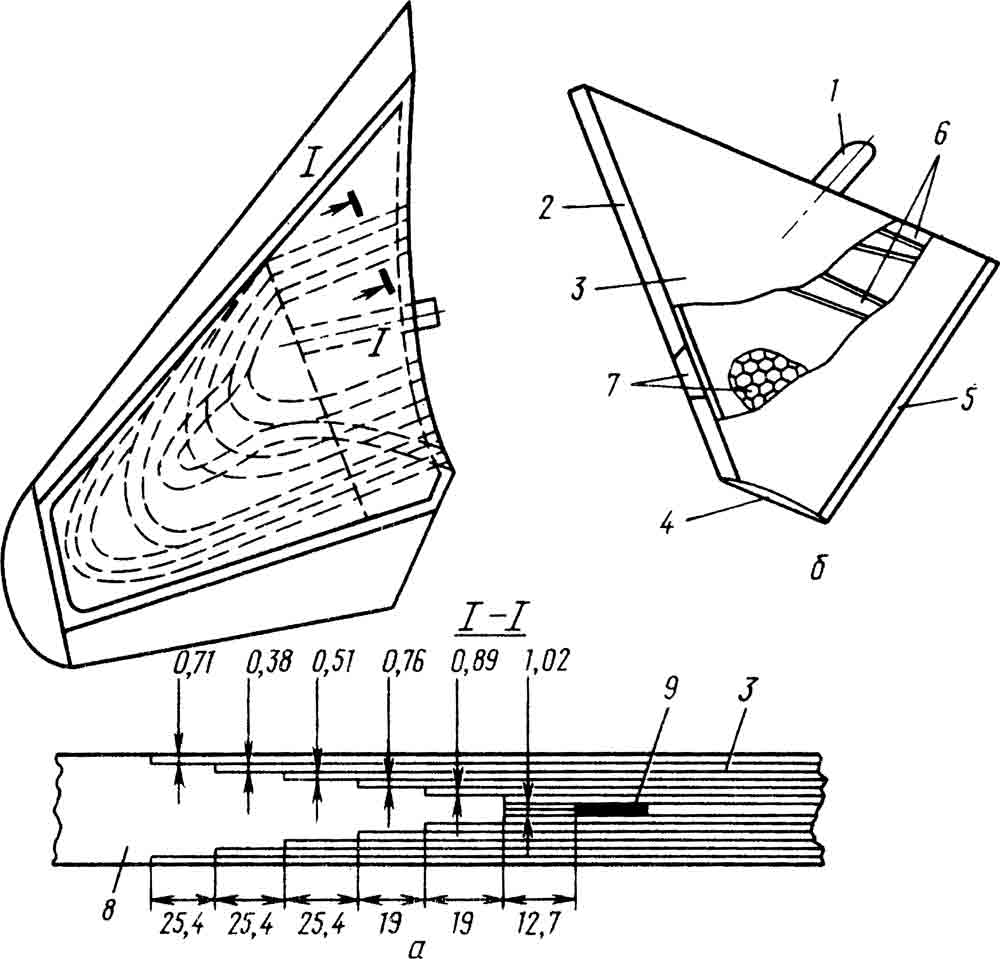 Рис. 1.4. Схемы укладки борных волокон в обшивке стабилизатора самолета F-14А (а) и конструктивный элемент обшивки (б) : 1 — ось поворота стальная; 2 — кромка передняя со стеклопластиковой обшивкой и сотовым заполнителем; 3 — обшивка со схемой укладки борных волокон 0 (60%)/ ±45° (30%)/90° (10 %); 4 — законцовка стеклопластиковая; 5 — накладка электропроводящая, соединенная с металлической осью для защиты от грозовых разрядов; 6, 8 — сплав титановый; 7 — соты; 9 — стекловолокно
На рис. 1.4, а (сечение І-І) показано шестислойное клеевое соединение боропластика с титаном, выполненное внахлестку. Это соединение характерно для зоны крепления шарнира узла поворота. Соединение рассчитано на нагрузку 267,5 МПа. Максимальное число боропластиковых слоев в этой зоне равно 56.
При статических испытаниях клеевое соединение нагружали при t = 150°С до разрушения. Разрушение начиналось в сотовом заполнителе, а затем приводило к локальному разрыву обшивки. Агрегат, подвергнутый испытаниям на усталость при типовых для самолета F-14А условиях нагружения, разрушился после 17000 летных часов. Разрушение произошло при нагрузках, увеличенных на 25% против эксплуатационных.
На самолете F-111F в шарнирной опоре крыла применены усиливающие накладки из ПКМ с боро пластиковым армирующим материалом (рис. 1.5). Такое конструктивное решение уменьшило габаритные размеры и массу шарнирного узла.
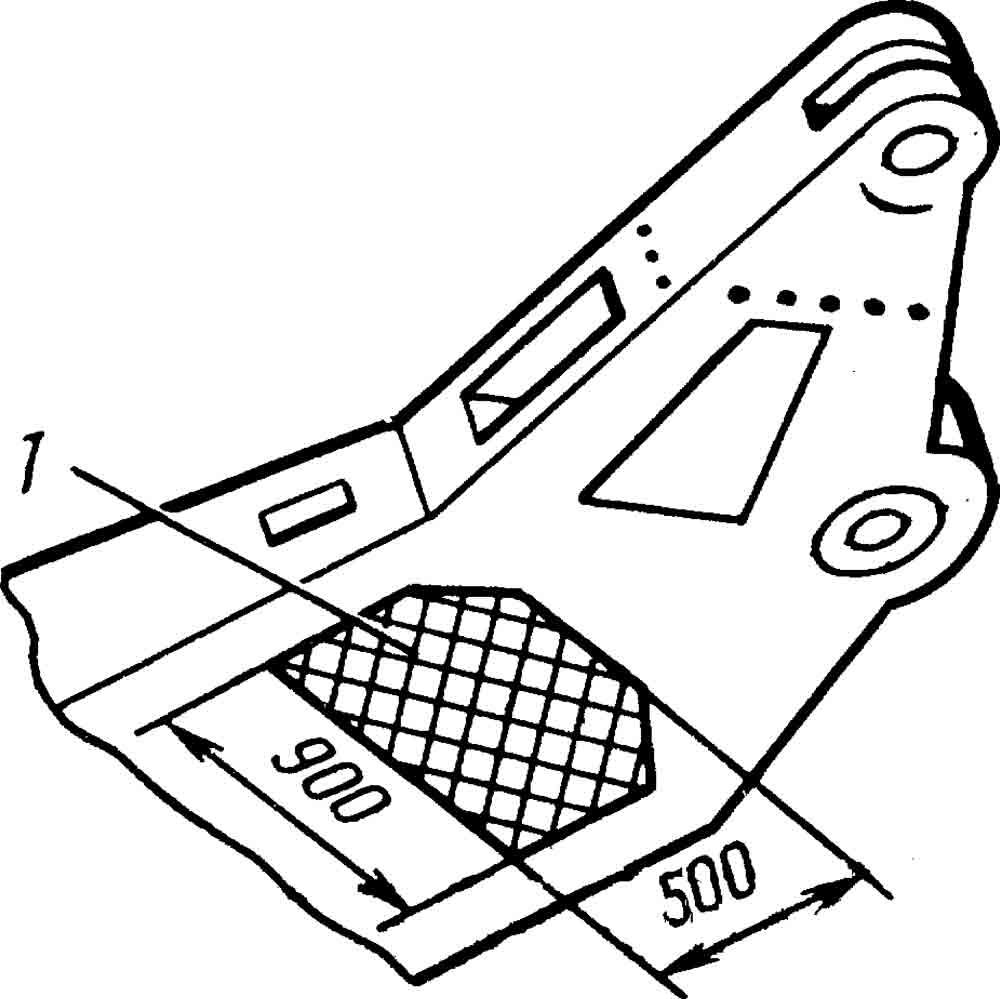 Рис. 1.5. Шарнирная опора крыла самолета F-111F: 1 — накладка из ПКМ с боропластиковым армирующим материалом
Фирма "Рокуэлл" применила ПКМ с боропластиковым армирующим материалом в конструкции агрегатов самолета В-1 для изготовления силовых лонжеронов фюзеляжа (рис. 1.6).
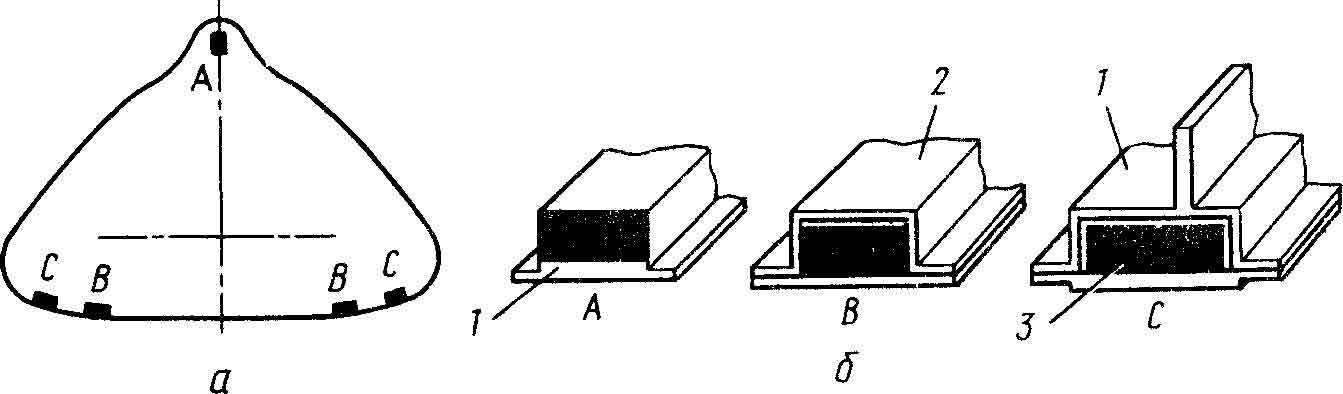 Рис. 1.6. Места расположения деталей из ПМК, с боропластиковым армирующим материалом в конструкции фюзеляжа самолета В-1: а — сечение фюзеляжа; б — сечение лонжеронов; А — лонжерон верхний; В — лонжерон нижний; С — лонжерон внешний; 1 — сталь; 2 — титан; 3 — ПКМ с боропластиковым армирующим материалом
ПКМ с боропластиковым армирующим материалом применяется для изготовления направляющих и рабочих лопаток турбин, оболочеқ компрессора ТТД, подкрепляющих элементов металлического силового набора планера, емкостей, рассчитанных для хранения газа под высоким давлением при температуре 200°С в течение 1000 ч, а также деталей разового действия. Необходимо иметь в виду, что длительный контакт с боропластиками при температуре нагрева 60...200°С не вызывает коррозии титанового сплава, но вызывает коррозию стали 30ХГСА. Прочностные храктеристики боропластиков очень чувствительны к изменению технологических режимов изготовления деталей: изменению давления (рис. 1.7) температуры и времени прессования (рис. 1.8).
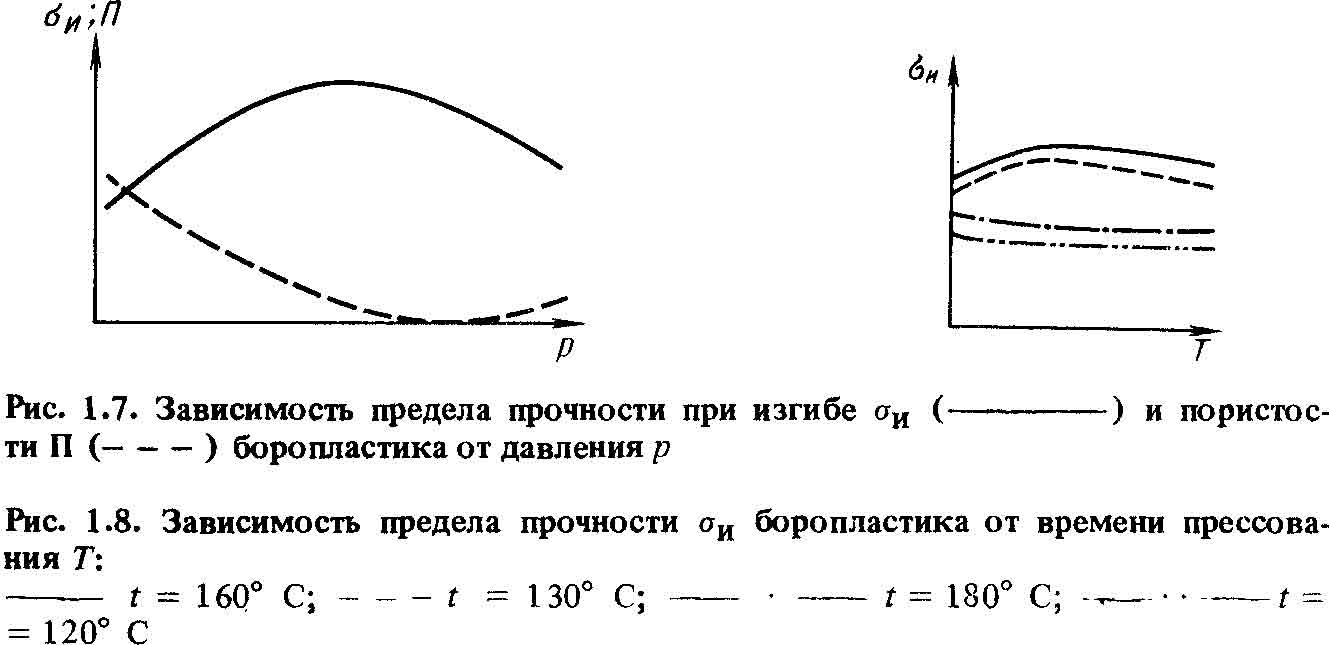
Число деталей из ПКМ с армирующим боропластиковым материалом в конструкциях самолетов быстро увеличивается со времени выпуска первых серийных стабилизаторов самолета F-14, масса которых составила всего 0,8 % массы самолета. Масса изделий из ПКМ с армирующим боропластиковым материалом в самолете AV-8B достигла 26% массы самолета. В табл. 1.5 приведены части самолетов, изготовленные из ПКМ с боропластиковым армирующим материалом.
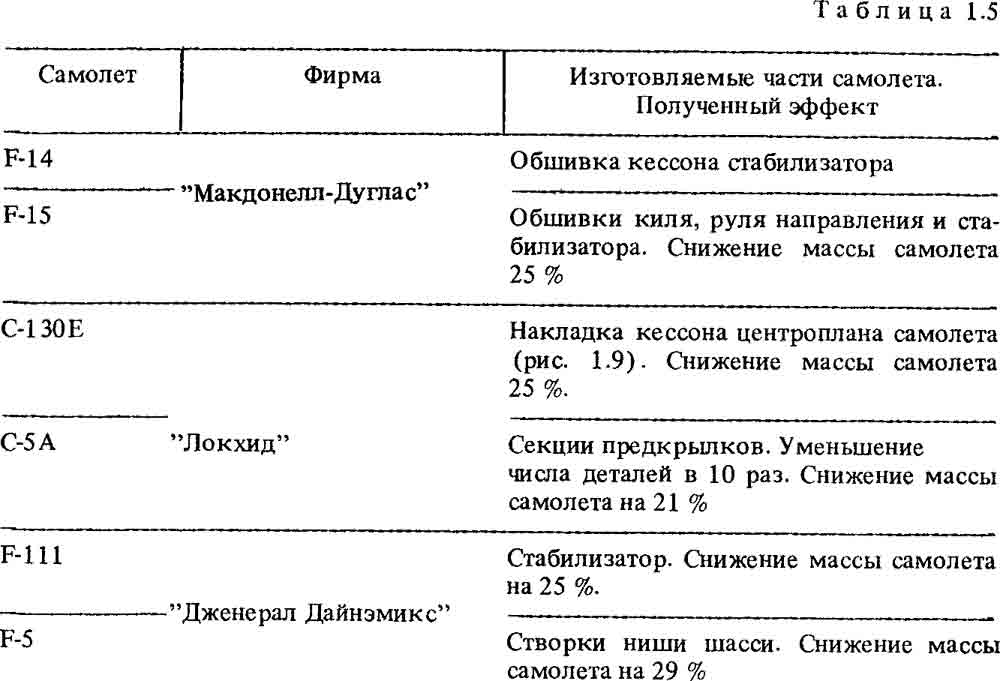
Производство агрегатов из ПКМ с боропластиковым армирующим материалом требует больших капиталовложений. Разработана модификация борного волокна — волокно борсик с покрытием из карбида кремния, нанесенным для повышения рабочей температуры.
Борное волокно используется также в ПКМ с алюминиевой основой, объемное содержание борного волокна в этих ПКМ 46...50%. Бороалюминиевый ПКМ применяется для изготовления трубчатых стоек средней части фюзеляжа транспортного космического корабля "Спейс шаттл". Такой материал применяется для изготовления панелей обшивки пилона на хвостовой части фюзеляжа самолета DC-10, что обеспечивает длительную работу при температуре до 177°С. Бороалюминиевые ПКМ применены для изготовления лопаток вентилятора двигателя реактивного самолета F-104. Этот материал обеспечивает поглощение энергии удара посторонними предметами.
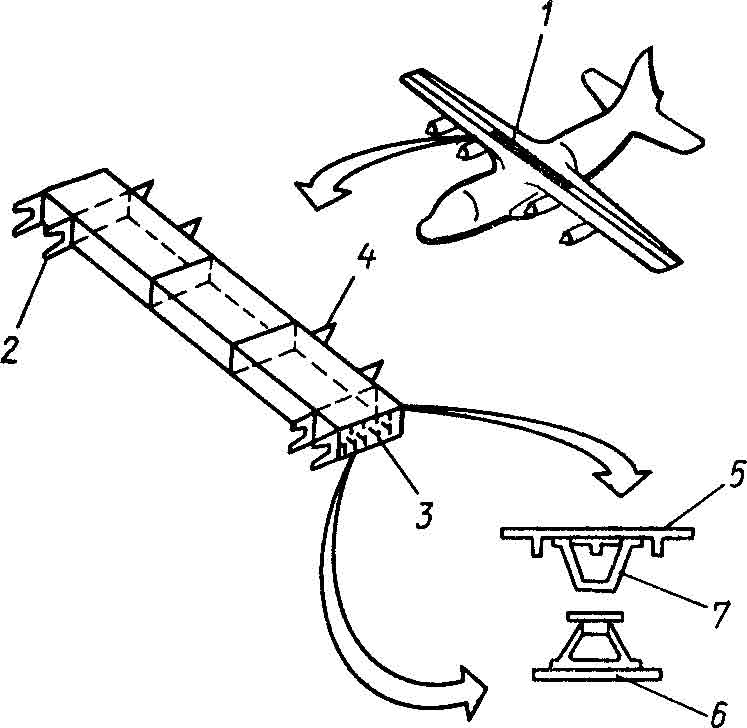 Рис. 1.9. Схема упрочнения кессона центроплана самолета С-130Е накладками из ПКМ с боропластиковым армирующим материалом: 1 - отсек топливный - кессон; 2 - узлы крепления пилонов двигателей; 3 —разъем технологический; 4 - узел крепления рельсов закрылков; 5 - накладка верхняя; 6 - накладка нижняя; 7 - детали из ПКМ
Фирма "Рокуэлл" разработала бороалюминиевый ПКМ, который применяется в конструкции крыла самолета В-1 для снижения его массы. Этот ПКМ имеет металлическую основу и армирующий материал из борных волокон с покрытием карбидом бора в сочетании с титаном. Это обеспечивает рабочую температуру волокон 540°С без снижения их прочности. Следует отметить недостатки ПКМ. Основным из них является коррозия, возникающая при контакте ПКМ с металлическими деталями, например при контакте углепластиков с алюминиевыми сплавами и обычной углеродистой сталью.
К другим недостаткам следует отнести необходимость экранирования радиоэлектронного оборудования и защиты от грозовых электроразрядов из-за низких электрической проводимости и теплопроводности ПКМ. Как одно из средств защиты от грозовых электроразрядов фирма "Грумман" предлагает на поверхность изделий путем полимеризации наносить полосы из медной фольги. Недостатком ПКМ на углепластиковой основе является малая устойчивость конструкции к ударным нагрузкам, а отсюда необходимость разработки технологии ремонта конструкций из ПКМ в условиях эксплуатации. Специалисты фирмы, выпускающей вертолеты Сикорский SH-53D, при создании балок вертолетов применяют волоконную оптику - волноводы, заполимеризованные в конструкцию балок. Указанные волноводы позволяют получить информацию о возможных повреждениях, возникающих в процессе эксплуатации. Световые сигналы, поступающие по волоконным волноводам, обрабатываются с помощью бортовых микропроцессоров и воспроизводятся либо на дисплее, либо с помощью речевого синтезатора.
Другой метод обнаружения повреждений основан на принципе акустической эмиссии. При этом методе акустические первичные преобразователи также путем полимеризации устанавливаются непосредственно в конструкцию изделия. Эти преобразователи изготовляются из поливинилиденфторидных полиметров, в которых при изменении давлений генерируются небольшие электрические заряды. Система преобразователей позволяет зарегистрировать трещину и определить ее местоположение либо методом триангуляции, либо по временной разнице между возбуждениями различных преобразователей. Частоту и амплитуду возбуждающих акустических волн сравнивают с типовыми значениями, заложенными в памяти микропроцессоров. Полученную информацию можно выводить на дисплей либо воспроизводить речевым синтезатором.
Для изучения структуры ПКМ обычно используются различные методы. С помощью микроскопов определяются объемное содержание фаз (основы и армирующего материала), диаметр волокон, их направление и распределение, пористость ПКМ (размер и форму пор), а также параметры процесса увеличения и возникновения новых дефектов при воздействии различных факторов (колебаний температур, влажности, ультрафиолетовой радиации и др.).
Исследования показывают, что структура ПКМ неоднородна: имеются области, ненаполненные основой, разнотолщинность прослоек основы между слоями армирующего материала, неравномерное распределение волокон и др.
ПКМ присущи две категории микродефектов: первичные, возникающие в процессе изготовления ПКМ и присутствующие в исходной структуре в виде пор, трещин, включений, отслоений, и вторичные, образующиеся в условиях эксплуатации под воздействием внешних факторов (влаги, нагрева, механических нагрузок, облучения и др.). В зависимости от места образования дефекты можно разделить на внешние и внутренние. Внешние появляются на поверхности ПКМ, а внутренние — внутри основы, армирующего материала и в пограничном слое между ними.
Наиболее типичные дефекты — поры, размер и форма которых, в первую очередь, определяются природой и свойствами основы и армирующего материала, а также технологией изготовления ПКМ. Основная причина образования пор — выделение газообразных продуктов при отверждении основы. Пористость углепластиков 1...3% (диаметр пор до 200 мкм), а пористость стекло- и боропластиков колеблется в более широких пределах. Так, пористость ПКМ с армирующим материалом типа стеклопластика и эпоксидными основами составляет 3...7% (диаметр пор до 400 мкм).
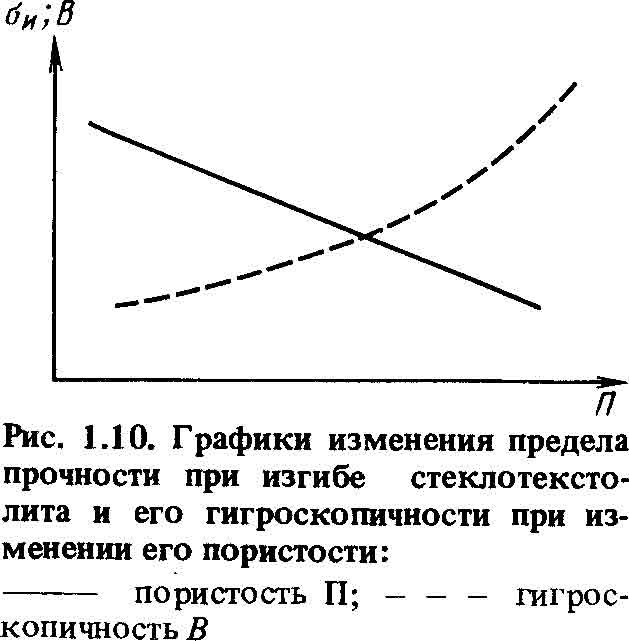
Большое значение имеет пространственное расположение слоев армирующего материала, которое определяет диаметр пор. Мелкие поры находятся внутри слоев, крупные — между слоями.
При изменении структуры ткани и тем более при переходе к нетканым основам характер пористости изменяется. Изменение пористости оказывает существенное влияние на механическую прочность ПКМ и их способность к водопоглощению. С ее увеличением прочность при изгибе уменьшается, а способность к водопоглощению возрастает. Согласно зависимостям, приведенным на рис. 1.10, предел прочности при изгибе σи и гигроскопичность В зависят от пористости П.
С помощью микроскопа можно исследовать строение границ между основой и армирующим материалом, а также поверхность армирующих волокон. Поверхности стеклянного, полимерного, углеродного и борного волокон имеют различные структуры. Если стеклянные волокна имеют ровную поверхность с микронеоднородной структурой, то полимерные волокна на поверхности имеют углубления вдоль оси шириной 0,2...0,3 мкм и длиной несколько микрометров.
Граница раздела между основой и армирующим материалом в ряде случаев монолитна и обеспечивает высокую прочность ПКМ. Однако встречаются участки неплотного прилегания армирующего материала к основе, которые уменьшают прочность сцепления слоев и ухудшают механические свойства ПКМ. Это явление характерно для ПКМ со стеклопластиковым армирующим материалом и с фенолоформальдегидной и кремнийорганической основами. Органостеклопластики обладают хорошими контактами с олигомерной основой и граница между ними выражена нерезко. Это связано с диффузией олигомерной основы в органостеклопластики.
Появление дефектов, ообенно микрополостей, на границе стекла и полимера ухудшает механические и диэлектрические свойства стеклопластиков. Обработка волокна адгезионно-активными замасливателями и аппретами, а также введение активных добавок в основу значительно повышает стабильность структуры и свойств стеклопластиков при увлажнении.
При сжатии стекло-, угле- и боропластиков в направлении армирования наблюдается сдвиг. Особенность разрушения органостеклопластиков в отличие от названных материалов состоит в том, что при растяжении и сдвиге они расщепляются вдоль оси органических волокон из-за высокой степени ориентации макромолекул и сравнительно слабой связи между фибриллами волокон. Вследствие низкой прочности органостеклопластиков при поперечном растяжении и продольном сдвиге они в отличие от других армирующих материалов практически не разрушаются по границе армирующий материал — основа.
При сжатии органостеклопластики в зоне разрушения не срезаются, как стеклопластики, а только изгибаются. Одним из путей повышения прочности является сочетание органических волокон со стеклянными, углеродными и борными, которое предотвращает хрупкое разрушение.
В.Н. Крысин и М.В. Крысин "Технологические процессы. Формования, намотки и склеивание конструкций" Москва "Машиностроение" 1989 |